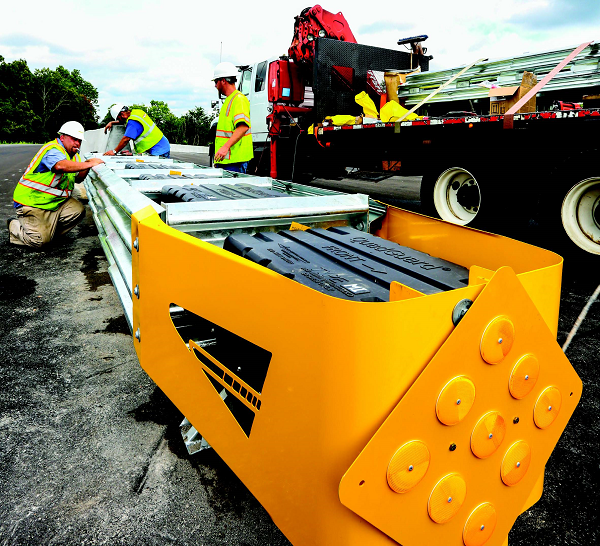
SAFETY TODAY: SHARED PERSPECTIVES
There are many common cores in construction, from scheduling and budget issues to material delivery and installation execution. An issue that is weaved in every industry on every job is safety. Although progress has been made, workers still suffer injuries on construction job sites across the United States, and the price that companies and workers pay for injuries is high. However, there are ways to reduce risks to decrease the professional, financial and personal burdens that injuries cause.
The Numbers
According to OSHA, 6.5 million people work at 252,000 construction sites per day in the United States. The agency says the construction industry’s fatal injury rate is higher than the national average in this category for all industries. There were 4,679 workers killed on the job in 2014. This is a 2% increase from 2013 and based on preliminary data (final 2014 statistics are expected from the Bureau of Labor Statistics this spring). That is about 90 deaths per week or more than 13 deaths per day. Of those deaths, 789 Hispanic or Latino workers were killed from work-related injuries. Of all fatal work injuries, those involving contractors accounted for 17%. Out of 4,251 worker fatalities in the private industry in 2014, 874 (20.5%) were in construction. The causes of death from the highest to lowest category are: falls, electrocution, struck by object and caught-in/between.
What to Report
One way to decrease these numbers is to report current incidents and learn from them. How do you know what to report? The simple answer is everything. True injuries, accidents, fatalities and illnesses create statistically significant data that allow trends to be followed and studied. Even near misses should be reported because they can shine a spotlight on a hazard that could turn into something more serious in the future. The only thing you should ever leave out of incident investigations and reporting is blame. Playing the blame game can decrease employee morale, reduce productivity and create a negative work culture. If workers don’t feel comfortable in presenting problems to management, they are going to hide potentially disastrous situations. When gathering information after an incident, OSHA suggests asking:
- Why was a procedure or rule not followed?
- Did company pressure jeopardize safety?
- Are procedures out of date?
- When did training last occur, and are updates needed?
- Has this incident happened in the past? If so, what is missing in safety protocol?
Resources
Both large and small companies have resources available to help them manage risks. OSHA has developed a website (osha.gov) to give employers and workers help to identify, reduce and eliminate construction-related hazards. OSHA also has a site (osha.gov/workers/index. html) designed just for workers so that they understand their rights and have a defined reporting method. The National Safety Council has a guidance document about how to conduct an incident investigation at www.nsc.org. Another avenue to promote safety is to look into Safety Week 2016, taking place May 2–6. The initiative was started by 40 national and global construction firms making up The Construction Industry Safety Initiative and the Incident & Injury Free Executive Forum. Many companies celebrate their own Safety Week and use the event as a way to refocus safety plans, come up with new safety tips and practices, and reinvigorate workers about the importance of safety. There also will be a Safety Summit in September by CISI to further promote safety. Find more details at www.safetyweek2016.com.
Sneak Peek
Safety is a broad topic, but this special section offers tips. If you are a highway design, bridge or safety engineer, you regularly consider safety features used on highways. The AASHTO Manual for Assessing Safety Hardware (MASH), is the new standard for the crash testing of safety hardware devices used on the National Highway System. Although AASHTO announced changes to MASH years ago, sunset dates were announced by the Federal Highway Administration in January. Turn to page S7 to discover more about those dates.
Of the changes, Jim Crowley, vice president of new product development and marketing for Trinity Highway, Dallas, says, “We fully support the AASHTO/FHWA agreement to transition to the MASH testing criteria. We have and will continue to develop products to the new testing standards in order to support the states and the implementation dates.” When looking for more safety tools, consider heading to your smartphone, computer or tablet. SafetyNet automates the collection of workplace safety data and predicts high-risk areas where injuries are likely to occur with 97% accuracy (see page S5).
Does It Matter?
Throughout the year, Engineering News-Record covers a wide range of industries, from bridges and highways to airports and ports. In all of these and other markets, construction workers regularly are engaging in activities that pose a risk, and every day management and workers are trying to figure out how to keep sites safe. The efforts that employers and workers make in setting safety practices and following them have made an impact. OSHA notes that since 1970, workplace fatality rates have decreased by 66% and occupational injury and illness rates have dropped by 67%. This data becomes even more statistically significant when you consider employment in the United States has doubled in 45 years. It is reassuring to know the joint efforts of workers, employers and regulating bodies do make a difference.
Ahead of the Curve with Roadside Hardware
In 2009, AASHTO introduced new testing criteria for roadside hardware with the Manual for Assessing Safety Hardware (MASH). MASH provides testing guidelines like NCHRP Report 350 but takes today’s vehicle fleet and road designs into consideration. While much of MASH’s testing criteria remains the same as Report 350, there are some significant changes, including:
- Small car mass and impact angle
- Pickup truck mass and center of gravity
- Impact angles for terminals and crash cushions
- TL-4 vehicle weights and speed
- Vehicle occupant damage
- Hardware modification notifications
In January, the Federal Highway Administration announced sunset dates for new installations of NCHRP Report 350 products. The following dates detail the last day a new Report 350 system for the corresponding product category will be available for letting on the National Highway System.
- Dec. 31, 2017: W-beam guardrail, permanent concrete barriers
- June 30, 2018: End terminals
- Dec. 31, 2018: Crash cushions
- Dec. 31, 2019: Everything else (TMAs, barricades, sign posts, etc.)

Trinity Highway’s engineering group is ahead of the curve, working on the evolution of many Report 350 products to MASH. Trinity Highway currently offers two MASH crash cushions in its QuadGuard Family of products: the QuadGuard M10 and the QuadGuard Elite M10. The QuadGuard M10 consists of an engineered steel nose and crushable, energy-absorbing cartridges. The Quad Guard Elite M10 consists of a flex-belt nose and potentially reusable cylinders. Both systems are MASH Test Level 2 and 3 compliant as redirective, non-gating crash cushions. Although the crash cushion sunset dates are not until the end of 2018, several states have taken a proactive approach. Oklahoma, Tennessee, Massachusetts and Michigan all currently have QuadGuard M10 or QuadGuard Elite M10 systems installed.
Source: ENR Magazine